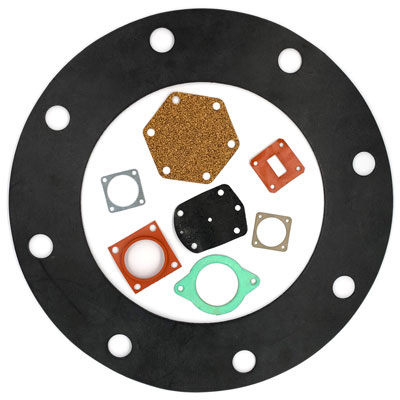
Gasket Seals
Premier North American Gasket Manufacturer
Sealing Devices is a leading gasket manufacturer in North America partnering with premium suppliers to offer a variety of gasket products. Our manufacturing facility includes over 200-pieces of equipment and in-house tooling and die-making, which allow us to make and distribute a number of gasket types, including metal gaskets, compressed sheet gaskets, and flexible graphite and most any other material with quick cut options.
Our Trusted Suppliers
We have partnerships with the industry’s top gasket suppliers including Garlock, Flexitallic, KLINGER Thermoseal, and more. Our relationships with these suppliers ensure that we can provide reliable and high-quality gaskets that fit your specific application needs.
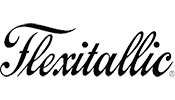
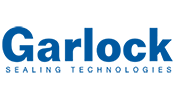
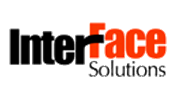
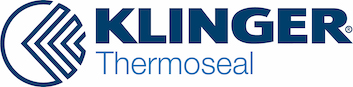
What is a Gasket?
Gaskets seal between two different surfaces under compression. Gasket sealing is a result of compressive forces created by sufficient bolt load and works to fill the imperfections on the mating surfaces to be sealed (ANSI Flange Standards). To help you choose the right gasket material for your application, you can rely on our applications engineering team for technical support recommendations. Learn more about our fabrication and converting capabilities.
Gasket Types
We offer several types of gaskets for high and low-temperature applications, including:
- Commercial Rubber
- Mil-spec Rubber
- Compressed Sheet Gaskets
- Cloth Inserted Gaskets
- Grafoil
- PTFE
- ePTFE (Teflon)
- Beater Add
- Metallic
- Sponge
- Foam
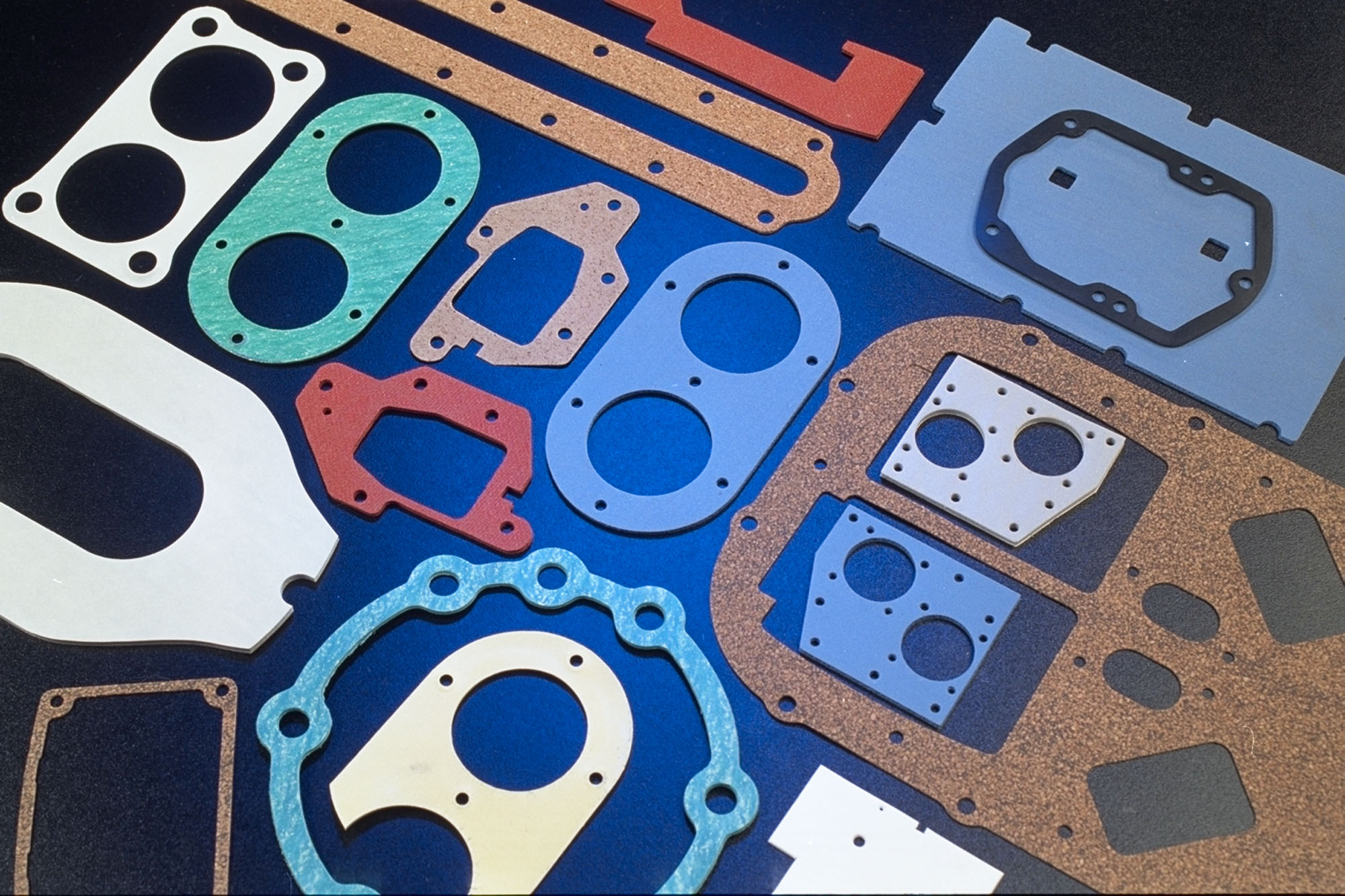
Gasket Products
Flexible Graphite Gaskets
GraFoil ® Flexible Graphite Gaskets provide superior performance in high-temperature sealing applications.
Spiral Wound Gaskets
Spiral Wound Gaskets are ideal for high-temperature applications needing resistance to corrosion.
Metal & Metallic Gaskets
Metal & Metallic Gaskets are ideal for Sealing Higher Temperature and Pressure Applications.
Compressed Sheet Gaskets
Compressed sheet gasket materials provide outstanding die-cut gaskets for superior sealing.
ePTFE (Teflon) Gaskets
ePTFE expanded Teflon provides extreme sealing in sheet gasketing, gasket tape, joint sealant, and universal gasket configurations.
Expansion Joints
Garlock Expansion Joints offer superior performance, reliability, and service life, resulting in improved plant safety and increased mechanical integrity of equipment.
Beater Add Gaskets
Sealing Devices is a converter of beater-addition (beater-add) gasket materials. These beater-addition gaskets address a wide range of performance capabilities and requirements.
Geltek
Geltek pre-cured silicone gels are die-cuttable solid gels with liquid characteristics.
NSF-61
Sealing Devices is a certified manufacturing facility that cuts, repackages and distributes NSF-61 certified gaskets for use in the drinking water treatment market.
Why Choose Sealing Devices As Your Gasket Supplier?
Custom Configurations: At Sealing Devices, we specialize in custom gasket configurations tailored to your specific applications, leveraging our in-house tooling, a wide range of materials, and precision manufacturing capabilities.
Commitment to Quality: We partner with premium suppliers and adhere to stringent quality standards, ensuring that our gaskets deliver consistent performance and long-term durability.
Industry Expertise: With years of experience providing effective gasket solutions, Sealing Devices offers expertise across a wide range of industries.
Engineering Assistance: The engineers at Sealing Devices are available to assist you with your next gasket installation. Our applications engineers offer multiple services to ensure your gasket solution is the right fit, including design assistance, material testing, and more.
Your Industry Leading Gasket Supplier
Sealing Devices brings decades of expertise to manufacturing and distributing high-performing gaskets trusted across various industries including aerospace, industrial, electronics, and more. Whether you require standard or custom gaskets, our team is dedicated to delivering solutions that enhance reliability, efficiency, and performance.